A rendszer által ellátandó általános funkciót részfunkciókra, azokat pedig elemi funkciókra bontjuk. A köztük lévő kapcsolatok kölcsönösen és hierarchikusan valósulnak meg.
A géprendszer egésze által ellátott funkció az általános funkció. A géprendszeren belül funkcionális és zavaró alrendszerek vannak. Funkcionális alrendszerek lehetnek: geometriai, kinematikai, energetikai, kommunikációs-információs, anyagi alrendszerek stb. Zavaró alrendszerek lehetnek: statikus és egyéb deformációk, dinamikus instabilitás, kopás, zaj stb.
Ha a rendszer változó hatású környezetben működik, ami a rendszer működési folyamataiban is zavarokat okoz. A zavar miatt olyan veszteségek lépnek fel, amelyek csökkentik a rendszer hatásfokát, és a rendszert a megengedett üzemi feltételeken kívülre juttatják. A rendszerállapot olyan adathalmaz, amely teljes körű információt ad a rendszer adott időpontban és adott környezeti feltételek melletti viselkedéséről az idő függvényében.
A rendszer alapállapotát a cél feladat paramétereinek időben történő megfigyelésével határozzuk meg. A cél feladat paramétereinek megengedett határokon belüli megváltoztatása határozza meg a rendszer kielégítő állapotát, ami azt jelenti, hogy a rendszer sikeresen látja el az előlátott feladatot. Mindaddig, amíg a rendszer sikeresen ellátja feladatát, addig biztosítottak a megfelelő kimeneti értékek. A rendszer hibás állapota azt jelenti, hogy a funkcionális alrendszerek és elemek között lévő kapcsolat és ezek jellemzői meghibásodnak és szükséges a rendszer megfelelő állapotba, azaz működőképes állapotba való visszaállítása. Ezt különféle karbantartási eljárásokkal érik el.
Részfunkciók az energiafelhasználás folyamatában
Minden géprendszerben a bevitt energia felhasználásával valósul meg a hasznos munka vagy egy bizonyos funkció elvégzése. Ebben a vonatkozásban a munkavégzés során nem mozgó gépek, mint például a gyártógépek (szerszámgépek), a vegyipar, élelmiszeripar, a textilipar és számos más iparág géprendszerei többnyire elektromos energiát használnak. Általános szabály, hogy a villanymotorokban mechanikai energiává alakul át az elektromos energia. A működés közben mozgó géprendszerek, mint a közúti járművek, hajók, repülőgépek, traktorok, munkagépek stb., az üzemanyag vegyi energiáját használják fel, amelynek a belső égésű motorokban történő égése először hőt termel, majd átalakul mechanikai energiává.
A motorok tervezésének alapvető felfogása, hogy az adott energia előállítására az minél kisebb legyen. Ebből kifolyólag a motoroknak nagyobb szögsebességgel és kisebb nyomatékkal kell rendelkezniük. Mivel azonban a gépi rendszerek végrehajtó szervei leggyakrabban kisebb szögsebesség és nagyobb nyomaték mellett tudják sikeresen ellátni feladatukat, szükség van a mechanikai energia állapotának megváltoztatására. A gépi rendszerek azon részei, amelyekben az energia állapota, azaz a szögsebességek és a nyomatékok nagysága változik, azok az áttételek. Az energia átadása a motor tengelyéről a végrehajtó szervbe állapotváltoztatás nélkül vagy váltómű, vagy egyéb átviteli elemekkel (tengelykapcsolók, közbenső tengelyek stb.) valósul meg. A funkció jobb elérése érdekében bizonyos gépi rendszereknek rendelkezniük kell bizonyos mennyiségű tárolt, felhalmozott energiával. Például a hidraulikus rendszerekben a folyadék egyenletesebb áramlását nyomástároló (hidraulikus akkumulátor) segítségével érik el. Így az energia a végrehajtó géprendszerekben egyik formából a másikba átalakulhat, megváltoztathatja állapotát, átvihető egyik helyről a másikra és felhalmozódhat. Ezen energiaváltozási folyamatok mindegyike egy funkció a rendszerben. A végrehajtó rendszerek funkciójától eltérően az energiarendszerek funkciója elsősorban az energiaátalakításon alapul.
A vízerőművekben a vízturbinákban áramló víz potenciális és mozgási energiája mechanikai energiává alakul, amelyet elektromos generátorok segítségével alakítanak át elektromos energiává. A hőerőművekben a tüzelőanyag vegyi energiája az égés során hőenergiává alakul át, amely a víz melegítésével gőz formájába kerül és a gőzturbinát meghajtva a mechanikus energia a generátorokban elektromos energiává alakul. Az atomerőművekben a fűtőanyag atomenergiáját hővé alakítják, amelyet a hőerőművekhez hasonlóan tovább hasznosítanak.
Részfunkciók a feldolgozási folyamatokban
Minden géprendszerben van egy anyag, a szó legáltalánosabb értelmében, amely annak a feladatának a tárgyát mutatja be, vagy amely által a rendszer funkciója megvalósul. Szerkezetük, összetételük, állapotuk, alakjuk, eredetük és tulajdonságaik szerint az anyagok nagyon eltérőek lehetnek. Például a bányászati géprendszerekben a munkaanyag elsősorban az érc, az üzemanyagok a közlekedési eszközökben, a gyártógépekben a feldolgozott anyag. Az aktuális folyamat típusától függően amelyek a kívánt funkciókat látják el, az anyagok számos változtatáson, azaz feldolgozáson eshetnek át. Például a bányászati géprendszerekben a munkaanyagot (ércet) bányásszák, szállítják, zúzzák és tárolják további felhasználás és feldolgozás céljából.
A mezőgazdaságban gépekben a munkaanyag lehet a gabona, amelyet aratnak, szállítanak, majd tárolnak. A vegyipar az alapvető anyagokból kémiai folyamatok által új, eltérő összetételű, szerkezetű és tulajdonságú termékeket állítanak elő. Ezek a példák azt mutatják, hogy a munkafolyamat során a munkaanyagok változhatnak forma, szerkezet, kémiai összetétel, hő- és egyéb viszonyok, átadandó, tárolás. Mindezek a változási folyamatok részfunkciókat képviselnek. Az üzemanyag (szén, olaj, gáz) mint hajtóanyag a géprendszerekben fizikai és kémiai átalakulásnak, állapotváltozásnak, szállításnak és tárolásnak vannak kitéve.
A felsorolt anyagokon kívül a géprendszerek olyan anyagokat használnak, amelyek általános alkalmazásúak, azaz lehetővé teszik a rendszer egyes elemeinek működését, a rendszer általános funkciójától függetlenül, például csúszó- és gördülőpárok kenésére szolgáló kenőanyagokat. Ezek funkcionális anyagok, a munkafolyamat során más anyagokhoz hasonlóan megváltoztathatják állapotukat, átvihetők vagy tárolhatók. pl.: amikor csúszó vagy gördülő csapágyakat kennek az olaj kényszerkeringetésével a szivattyúban, az olajat egy bizonyos nyomásra összenyomva, a kenési helyre eljuttatja, ahol ellátja feladatát, majd visszavezetik a tartályba. Ezek a részleges kenési folyamatok képviselik a géprendszer részfunkcióit.
A géprendszerek vezérlésére használt részfunkciók
A géprendszerek kezelése és ellenőrzése, a rendszer megfelelő működéséhez fontos munka- és hajtóanyagok, energia és alapelemek állapotának ismerete alapján valósul meg. Ezekre a feltételekre vonatkozó adatokat állapotjelzők közvetlen mérésével nyerjük, amelyek a fizikai mennyiségek, hőmérséklet, nyomás, sebesség, áramerősség, rezgés, alkatrészek deformációja, zaj stb. mérésére redukálódnak. Például a gép helyes üzemének elemzésekor, a kenési funkciók megvalósulásának ellenőrzése elsősorban az olaj paramétereinek figyelésével, valamint a nyomás és az olaj hőmérsékletének ismerete alapján történik a szükséges helyeken. A kenési alrendszerben, amely egy szívó- és nyomóvezetékkel ellátott szivattyúból, egy tisztítóból, olajhűtőből, tartályból szelepekből áll, általában a következő értékeket mérik: nyomás és hőmérséklet a nyomóvezetékben, némely esetben a kenési hely mögötti olajhőmérséklet, nyomásesés a szűrő előtt és után és a tartályban lévő olajszint. A mérési folyamat leggyakrabban az egyik energiafajtának a másikra való átalakításával, valamint bizonyos mérőműszerek használatával történik. Például a hőmérséklet mérésének legegyszerűbb módja a higanyos vagy alkoholos hőmérők használata, amelyek a hő hatására tágulnak. A hőmérsékletátadást a közegből a működő mérőanyag felé áramló hő átadásával érjük el. Az ilyen hőmérőket alacsonyabb hőmérsékleten és jól hozzáférhető helyeken történő mérésre használják. A mérések magasabb hőmérsékleten és a szabályozási ponttól távolabbi helyeken is mérhetők elektromos műszerek segítségével. Az egyik módszer azon alapul, hogy a vezető elektromos ellenállása a hőmérséklet függvényében változik. Ha olyan vezetőt használunk, amelynek hőállapotát az elektromos ellenállás változásának mérésével határozzuk meg, akkor a termikus állapotra, azaz a hőmérséklet nagyságára vonatkozó adatokat kapunk. A hőátadás folyamata, az elektromos jel továbbítása a vezérlőponthoz, valamint a jel vizuális vagy egyéb jelzővé alakítása, a gépi rendszerek vezérlésére használt részfunkció.
Elemi funkciók
A gépek teljes funkciója olyan elemi funkciókból áll, amelyek több különböző gépben is megtalálhatók. Az elemi funkciók mindegyike számos fizikai elven alapulhat. A lehetséges fizikai elvek felhasználásával több fizikai eszköz (mechanizmusok, gépek) tervezésére van lehetőség.

Minden gép és berendezés öt elemi funkcióval tervezhető, nevezetesen:

- közvetlen csatolás, például fogaskerekek
- laza csatlakozás, például szíj;
- teljes korlátozás, például csavar;
- részleges korlátozás, például csapágy és
- egységesítés, például sebességváltó ház.
Az összes funkcionális modul a következő hat alrendszerbe integrálható:
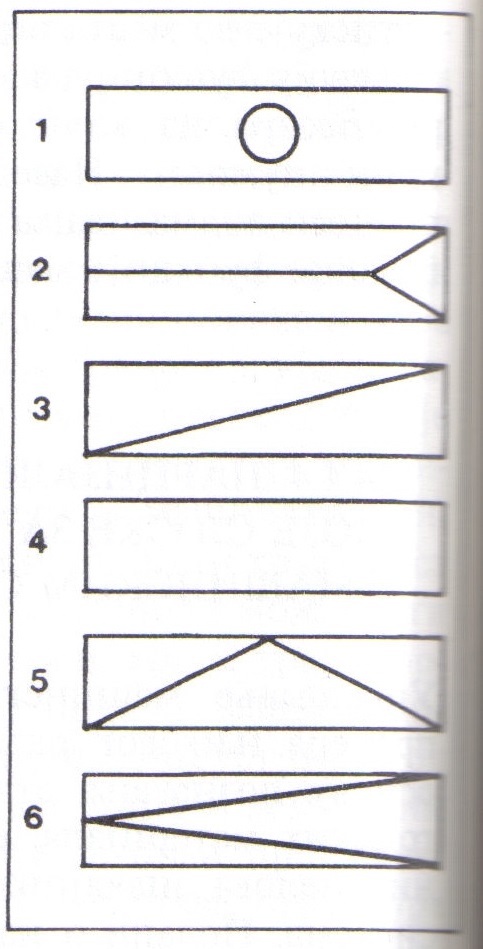
- felhalmozódás;
- elágazás;
- változás;
- irányítás;
- megbízás és
- variáció.
A logikai operátorok alkalmazhatók vagy nem alkalmazhatók a funkcionális modulokra, így minden funkcionális modulnak és alrendszernek több változata van. Így a rendszer funkciója többféle változatban is elképzelhető, amelyeket azután ki kell értékelni. Ezenkívül minden modulnak és alrendszernek megvannak a saját korlátai, amelyeken keresztül anyagot, energiát és információkat cserél a rendszer többi moduljával. A gépgyártás folyamatának kreatív része a megoldandó funkció struktúrájának meghatározása, valamint a megoldás legkedvezőbb változatának felmérése és kiválasztása.
Az tervezés minden egyes figyelembe vett modulja egy halmazból áll:
- információ a szabványos méretekről, a megfelelő anyagról, folyamatról stb.;
- a természeti törvények vagy a tapasztalat által meghatározott szabályok;
- tervezési paraméterek, amelyeket úgy kell megoldani, hogy az alkatrész (termék) teljesen meghatározott legyen és
- paraméterek (méret), amelyekkel egy modul szülő, párhuzamos vagy alárendelt hierarchikus kapcsolaton keresztül kapcsolódik más modulokhoz.
Az egyes modulok koncepcionális elemzése és megvalósítása szakaszosan történik, pl. az előzetes ötlettől (koncepciótól) kezdve, az ötlet kidolgozásán keresztül a teljes megvalósításig.
Rész- és elemi funkciók végrehajtói
A részfunkciók végrehajtói, azaz a gépi rendszerek azon részei, amelyek segítségével részfunkciókat valósítanak meg, a rendszer elemei alkotják. Ezek alrendszereket, csoportokat vagy összeállításokat képviselhetnek. A részfeladatokat végző részegységek fenti példáiban a mechanikai energia állapotát megváltoztató erőátvitel lehet a rendszer eleme vagy egy csoportja, a tengely a tengelykapcsolóval pedig egy csoport az energia átvitelére annak állapotának megváltoztatása nélkül. Az elemi funkciók végrehajtói a szerkezetek vagy a gépek elemei. A megadott példákban ezek a következők: tengelyek, tengelykapcsolók, tengelykötések, ékek, hornyok, szorítócsuklók, szíjak, fogaskerekek vagy egyéb elempárok.
Azok a gépelemek, amelyeket nem lehet roncsolás nélkül több részre bontani, egy géprendszer, gép vagy szerelvény alapvető részei.
A végrehajtás módja szerint a részfunkciók csoportokba sorolhatók. Az elemi funkciókat részfunkciókon belül látják el. A részfunkciók mindegyike olyan elemi funkciók végrehajtásával valósul meg, amelyek különböző módon kombinálhatók vagy megfelelő szerkezetbe kapcsolhatók. Például mindegyik csapágy különálló vagy központi kenéssel rendelkezik. Az emelő hajtómechanizmusában lévő tengelykapcsoló-fék tengelykapcsolóra és fékre bontható, amelyek mindegyike ellátja a maga részfeladatát. Az elemi funkciók felépítése akkor a legegyszerűbben kialakítható, ha ezek mindegyike egy gépelem segítségével végrehajtható.